iESN BGA Rework Station - The Concept
Before the iESN Workbench, before the simulator, before cold assembly —
there was this problem:
How do you actually rework a BGA… without guessing?
The industry pretends it solved this 20 years ago.
But all it did was package convection ovens in smaller boxes and sell them with bigger promises.
And for 40 years, professionals have been stuck between two lies:
Fake thermal profiles that never match reality
Machines that “work” only when you’re lucky
So we started here.
Not because it was easy. But because it was the most broken — and the most essential.
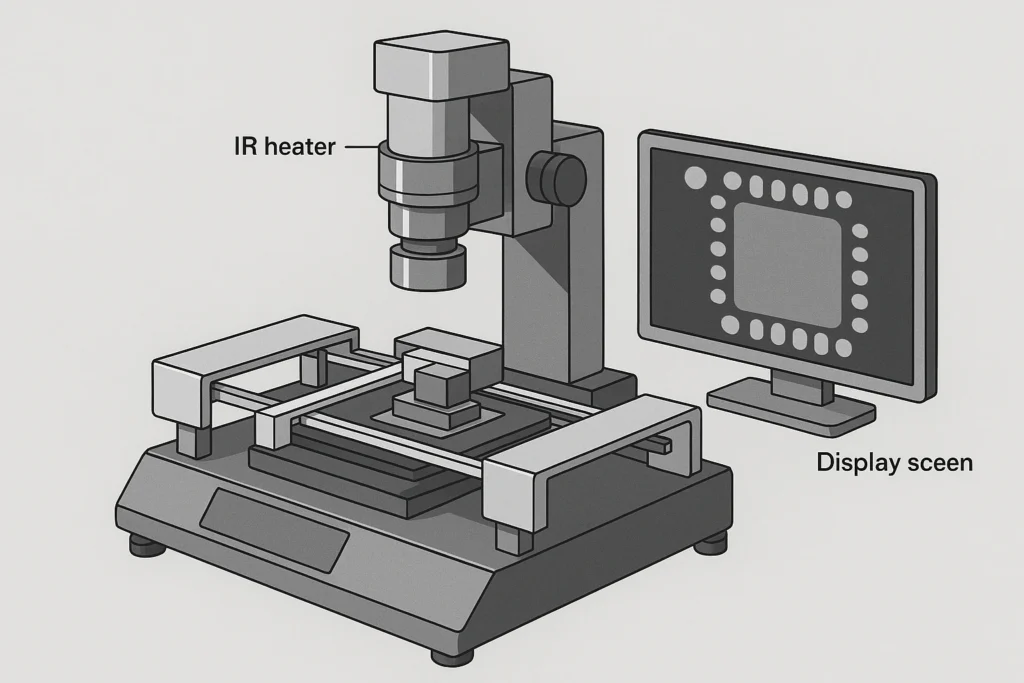
The Industry Illusion
They call them “professional BGA rework stations.”
They cost thousands. They promise precision.
And they’ve been wrong since the day they were built.
Most are just glorified hot air guns inside a metal box.
Wrapped in plastic. Sold with buzzwords.
No physics. No control. No repeatability.
They give you:
Turbulent airflow that shifts with ambient temperature
Fake thermal “profiles” that ignore material mass, heat sinks, copper planes
Open-loop systems that burn boards while pretending to follow a curve
Webcam-grade cameras sold as alignment systems
No thermal feedback. No scientific documentation. No trust.
And yet — they’ve become the standard.
Not because they work.
But because everyone else gave up trying to make something better.
The Physics-Based Rebuild
We didn’t want to make a “better machine.”
We wanted to erase the lie — and rebuild from physics up.
So we asked the only question that matters:
What does a BGA rework station need to be, if it’s going to work every time — without luck?
The answer wasn’t in software.
It was in heat transfer.
Not simulated, not guessed — but measured, controlled, real.
We stopped thinking like product designers…
and started thinking like thermal engineers.
That’s why the iESN BGA Rework Station began with:
-
A top heater that doesn’t transfer heat — it transfers pure energy.
No moving air. No thermal mass. Just directional electromagnetic energy.
The chip itself transforms the energy into temperature —
because temperature is the result, not the input. -
A non-contact IR sensor system — dynamically calibrated to perfection.
Calibrated against NIST standards, not approximated.
Able to detect real temperature across any material: black plastic, bare silicon, metal cap, PCB substrate.
This isn’t a guess — it’s a traceable measurement system. A high-resolution infrared thermal camera — not for marketing, but for real-time thermal feedback
A bottom heater that also transfers pure energy — not heat.
Built from dense halogen arrays, delivering radiation-dominant energy across the board’s volume.
It is the PCB itself that transforms that energy into heat —
based on its geometry, copper mass, and internal structure.A CNC-stable platform — to eliminate vibration, shift, and mechanical drift
No airflow, no turbulence, no plastic shielding — just pure control
This isn’t theory.
This isn’t about heating.
It’s about how science moves energy — and how we’ve finally learned to use it.
Zero inertia. Maximum precision.
This is energy transfer — aligned with physics, not marketing.
What Makes It Work
-
Cylindrical top energy source
Pure radiant energy — no airflow, no turbulence, no contact.
Not focused. Not sharp.
But perfectly diffused to ensure uniform energy delivery across the full chip area.
The chip becomes the sensor — not the software.
Every shape, every package, every material receives exactly what it needs — no more, no less.
-
Bottom halogen array
Radiation-dominant. Ultra-fast. Responsively engineered.
No warm-up cycles. No preheating. No thermal inertia.It delivers pure energy, not heat —
and the PCB itself transforms that energy into temperature,
based on material, geometry, and copper mass.This is not convection. This is not approximation.
It’s energy transfer — obeying the same scientific laws as the top system,
creating perfect thermal alignment from both sides. -
Real-time thermal feedback
A scientific thermal camera and NIST-calibrated infrared sensors working in tandem.
Not approximated — but traceable. Certified. Verified.Every reading is part of a closed-loop control system,
backed by a NIST-traceable ±1°C accuracy standard.Powered by a fuzzy-logic PID algorithm with AI-assisted correction layers,
the system constantly adjusts in real time —
not based on assumptions, but based on the material’s actual energy absorption behavior.No delays. No guessing. Just physics. Measured, learned, and applied.
-
Closed-loop control system
Every energy change creates a measurable material response — and that response shapes the next pulse.
No blind “profiles.” No open-loop failures.
-
CNC platform architecture
Stability, repeatability, and alignment.
A system that remembers where it started — and lands exactly where it should.
-
No airflow, no heaters, no fans
Nothing that pushes heat.
Only elements that deliver energy, and let physics do the rest.
-
Precision Optical Alignment System
-
High-precision optical alignment system
Not based on beam splitters (as “professionals”) pollute all over the internet proving the ignorance about scientific terms — but on beam combining.
We don’t split your eyes in two — we unify two optical axes into a single, undistorted image, the corect – scientific term is “beam combiner” not “beam splitter“.You don’t have to “guess the center” between two half-aligned views.
You see one image. One real focal plane.
One decision. One result. In parallel, the system includes the only true camera/s positioning platform
No beam combiners. No complex optics. No dependency on external calibration.
Just clean mechanical symmetry — and full control of your visual perspective.To place the chip on the board?
Of course — the system includes a true P&P (Pick and Place) module,
engineered to automatically position the chip with micrometer precision.
Not by hand. Not by tweezers.
But by a repeatable, software-controlled system aligned to the optical axis.
This is not internet-grade “professionalism.”
This is optical engineering, grounded in physics — not fiction. -
Why It Took So Long
Because no one wanted to build it.
Not the factories.
Not the brands.
Not the “professionals” selling hot air and blind profiles for decades.
Building this system wasn’t hard because the idea was complex —
It was hard because the entire industry was built around ignoring the problem.
We started in 2012 thinking we could solve it quickly.
We were wrong.
What followed was over a decade of:
Burning boards
Failing sensors
Wrong materials
Fake specs
Rejected patents
Relearning physics the industry pretended it already knew
It wasn’t the science that slowed us down —
It was the weight of misinformation we had to burn through first.
There was no book on how to build a real BGA rework station.
So we wrote it.
Because behind every unsolved repair…
behind every “unfixable” module…
behind every overpriced, underperforming station…
There was a simple truth:
No one had ever really tried.
Until now.
Final Statement
This isn’t a “BGA rework station”.
It’s the end of pretending.
The end of burned boards and guessed profiles.
The end of hot air, fake specs, and empty interfaces.
What you see here is not a product.
It’s a physics-aligned, measurement-based system —
built to bring real professionals back into control.
You don’t need luck.
You don’t need workarounds.
You don’t even need hope.
This is The BGA Rework Station
You need this.