No Reflow. No Vapor. – The Concept
The Myth of Progress
They told us reflow was progress.
That heating every board to 250°C, pushing it through an oven, and watching the plastic survive — was how real electronics were made.
Then came vapor phase: “gentler,” “more controlled,” “safer.”
They sold us that too — as if swapping heat for vapor made it intelligent.
But it was all the same story:
Stress the board
Hope the components stay aligned
Pray the solder doesn’t wick
Waste kilowatts of energy to melt something for 8 seconds
You mix the surface tension of the agent
with the surface tension of the tin
It wasn’t science. It was thermal tradition.
So we did the only thing a real engineer would do:
We walked away.
No reflow.
No vapor.
No profiling.
Just the question:
What happens when you build soldering around precision — not temperature?
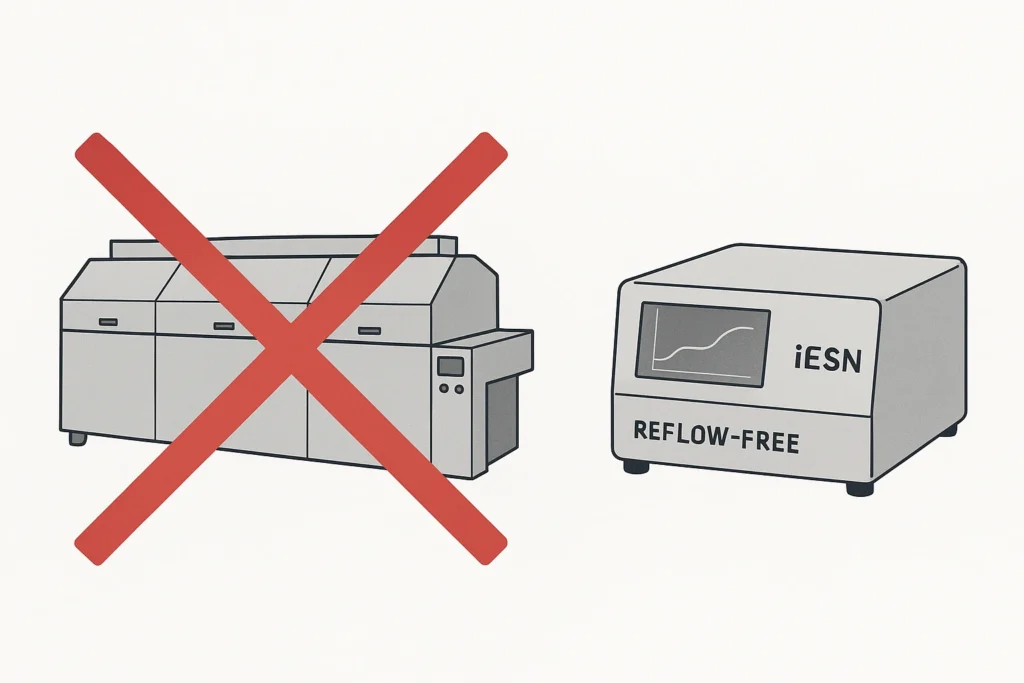
Why Reflow and Vapor Are Broken
Reflow and vapor systems were never built around physics.
They were built around tolerance — how much heat a board can take before it warps, shifts, or burns.
That’s not precision.
That’s gambling with melting points.
Here’s what’s broken:
Glass transition zones (Tg) — Every PCB has a temperature where its structure starts to degrade. Reflow ignores it. Vapor phase pretends it’s harmless.
Thermal shock — When components of different mass heat and cool at different rates, failure becomes inevitable.
Profiling guesswork — No two boards absorb heat the same way, yet you’re expected to “profile” them like they’re repeatable.
Energy waste — Kilowatts spent to raise an entire chamber to 250°C just to fuse 0.05g of solder.
Environmental cost — Massive ovens running 8 hours a day to process boards that could be soldered in 10 seconds.
No real-time control — Once you hit “start,” you watch and hope. There’s no loop. No intelligence. No feedback.
And the worst part?
The industry knows all of this — and still accepts it.
The Alternative
What if soldering didn’t require ovens?
Not 250 °C high heat.
Not profiled heat.
Just a completely different approach to how soldering works.
That’s the foundation of the iESN method.
We don’t heat the board.
We don’t stress the assembly.
We simply achieve soldering without using reflow or vapor.
The result?
No profiles
No hotspots
No thermal warping
No wasted kilowatts
We cannot disclose more details at this stage —
the process is in patent-pending status,
and based on a mechanism that has never been implemented in production systems.
This isn’t low-temperature soldering.
It’s a post-reflow transition —
quiet, clean, and measurable.
How It Works (Without Saying How It Works)
The iESN post-reflow method doesn’t rely on ovens, vapor chambers, or traditional heat transfer.
Instead, it operates within a carefully controlled physical window where:
Energy is delivered without heating the entire board
The solder reaches functional state without thermal overshoot
Joints are completed in 10 to 60 seconds — regardless of board size
The PCB remains under 50°C — always
There is no need for thermal profiling, preheating, or cooldown cycles
No external agents.
No chemical reactions.
No airflow.
Just controlled physics — applied only where needed, never where it causes harm.
Everything is monitored in real-time, recorded, and logged through the iESN system —
ensuring full traceability, documentation, and feedback across every soldered joint.
And because it works without reflow —
it works on boards that traditional methods would destroy.
Why It Changes Everything
his isn’t just a better soldering process.
It’s a fundamental shift in what’s possible.
With reflow and vapor, soldering defines the environment.
With the iESN method, soldering adapts to the environment.
Here’s what changes:
✅ Board design — no longer restricted by thermal limits or layer stress
✅ Component choice — sensitive or irregular parts can be used without fear
✅ Energy footprint — kilowatts become watts
✅ Environmental impact — no ovens, no heat chambers, no vapor fluids
✅ Manufacturing size — what once needed a line now fits on a desk
✅ Repair and rework — precision soldering is now possible anywhere, without danger
✅ Education and prototyping — no profiles, no thermal ramp-up, just direct logic and measurable behavior
What used to require an entire production setup —
now runs from a system you could carry under one arm.
This doesn’t scale down the process.
It rewrites the rules of the process.
And of course —
everything is fully traceable from start to finish through the iESN System,
with every action, signal, and result logged, timestamped, and iESN standards-compliant.
Certified to be perfectly compatible with all iESN workbenches, protocols, and future assembly workflows.
Final Statement
This isn’t a reflow upgrade.
It’s the end of ovens, the end of profiling, the end of waiting.
It’s not low-temperature.
It’s not semi-manual.
It’s not rebranded vapor.
It’s a new category —
born from real science, protected by real work,
and built to replace 40 years of thermal compromise.
The industry says, “That’s not possible.”
We say:
It’s already happening — and we can prove it.